Author: Professor Darwin Tat Ming Lau, Department of Mechanical and Automation Engineering
In recent years, the challenge of aging construction workers in Hong Kong is becoming increasingly severe. As of October 2023, the percentage of construction workers who are above 50 in age is approximately 45%. In particular, the portion of skilled construction workers above 50 in age is even higher at 63%. In recent years, there has been many unfortunate accidents related to work at heights and site safety. With 12% of all accidents in 2023 being related to work at heights, the demand for construction technology is greater than ever before. As such, the development of new technological solutions to improve construction safety, quality and efficiency is recognised and welcomed by the society’s building stakeholders, from government, building owners to developers, contractors and workers.
At The Chinese University of Hong Kong, the Centre of Robotic Construction and Architecture (CRCA) has been focusing on the development of autonomous robots that can meet the needs and demands of the Hong Kong construction industry. During our journey since 2018, the CRCA has been tackling two major challenges. The first is to identify the most suitable task(s) that robots can solve within the construction process. This is very important as the development of construction robots is both time-consuming and costly due to the complexity in operating within harsh construction site and the large scale of the robots required. The second is to establish an effective research and development, testing, deployment and ultimately commercialisation workflow in order to have the robots to operate in real-world construction. In particular, this involves working closely with building contractors, workers, building owner and various other stakeholders.
In this article, two example projects will be showcased to highlight the challenges, journey and corresponding solution within deploying construction robots within Hong Kong.
CUHK Yard for Environmental Sustainability Project
The CUHK YES project represents a real-world deployment of the CU-Brick cable-driven robot system for laying real bricks for a permanent structure. The YES pavilion is built at CUHK to house cabinets for recycling, up-cycling and freecycling to promote environmental sustainability. The CU-Brick robot is an 8-cable reconfigurable cable-driven parallel robot, with the capability in manipulating a gripper end-effector to a desired position and orientation accurately. Since 2017, the CU-Brick robot has been developed through multiple iterations through various demonstrations and exhibitions as a collaboration between the CUHK Department of Mechanical and Automation Engineering and Mr. Adam Fingrut from the CUHK School of Architecture. From a small-scale robot of 2m x 2m x 2m volume carrying small wooden bricks within indoor environments to ultimately a larger area system to manoeuvre larger and heavier real bricks outdoors at a real construction site, the system has undergone many improvements and redesign.
In the YES project, primarily challenges that our team had to overcome include: 1) design of reconfiguration of the lower attachment points of the cable robot to eliminate interference between the cables and structure; 2) improvement of robot components to be robust to operate outdoors under adverse weather conditions such as high heat and rain; 3) improving the system localisation and calibration to ensure high repeatability and accuracy within a large operation area; and 4) the construction workflow to meet the requirements in Hong Kong.
Some of its standout features of CU-Brick robot include:
- Wireless Gripper End-Effector – Ensures secure brick handling and precise placement.
- Collision-Free Workspace Planning – Workspace model adjusted for construction progresses, preventing interference with built structure.
- Reconfigurable Cable Attachments: A secondary elevation mechanism dynamically adjusts cable attachment points, extending the robot’s workspace and preventing interference with the growing structure.
- High-Resolution Localization – Integrates laser distance sensors and spatial mapping for continuous self-correction and calibration.
- Fiducial Marker-Based Calibration – Uses ArUco markers for real-time position tracking and error correction.
From January 2025, the CUHK YES project has begun the building process, and the structure was completed in April 2025. The YES structure consists of over 5,800 bricks over an area of approximately 9m x 13m and at 2.5m tall in height in 40 layers. In addition to the technology development, another challenge of the project to overcome was the collaboration with the building contractor and workers. This includes the statutory requirements, the determination of which tasks to be completed by the robot and the workers, and the planning of how they would cooperate. For example, to ensure that the brick layers are levelled and straight, the robot is responsible for accurately placing the brick while human workers will apply the mortar and do quality assurance. The project closely involved Hip Hing Builders Company Limited as the building contractor and Cundall as the structural engineering consultancy.
Beyond upgrading the design and function of the YES site, the robotic construction process shows the potential of using automation to increase the precision, accuracy and efficiency of construction methods. This project has attracted significant media publicity, along with guest visits from the industry, Construction Industry Council and the Development Bureau.
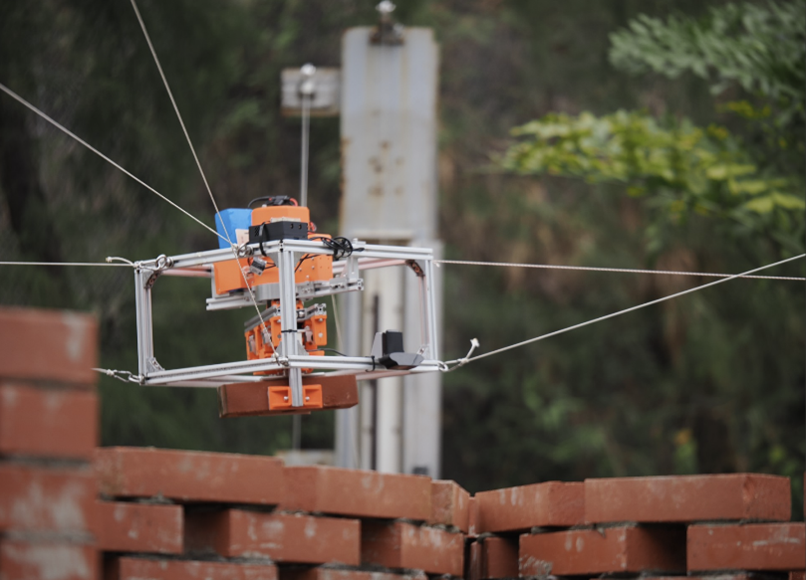
RoBosun Façade operation robot
Façade operations using robots, such as inspection, painting and repair works, are in critical demand due to ever increasing operational costs, safety concerns, aging workforce and lack of skilled workers. Existing façade operations robots are typically large and bulky, and struggle to handle complex non-regular façade surfaces. The RoBosun system is a new type of façade robot inspired by the bosun chair, that suspends the end-effector from a mobile robot located at the rooftop. Thus far, this robot has been developed for two different applications: a) hammer tapping; and b) painting.
This robot was developed since 2021 in close interaction with the Architectural Services Department and various maintenance contractors in Hong Kong, including Cheung Hing Construction Company Limited, Amain Engineering Development Limited, Sun Fook Kong Holdings Limited, Square Construction Company Limited. Rather than being developed solely within the laboratory, the robot was predominantly developed through a series of real-site tests. Through the tests, very important feedback and suggestions were provided by the government and industry. One noticeable example is the tapping procedure, where initially the robot would stop at each location to tap, analyse and then move to the next location, but through the recommendation of the contractors, the robot now conducts the inspect during continuous descent to increase the operating efficiency.
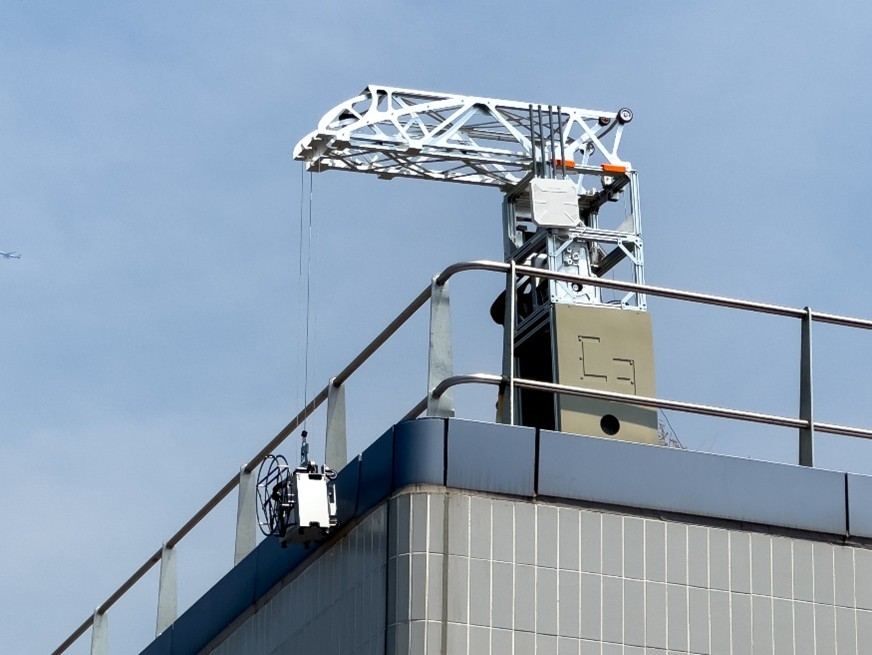
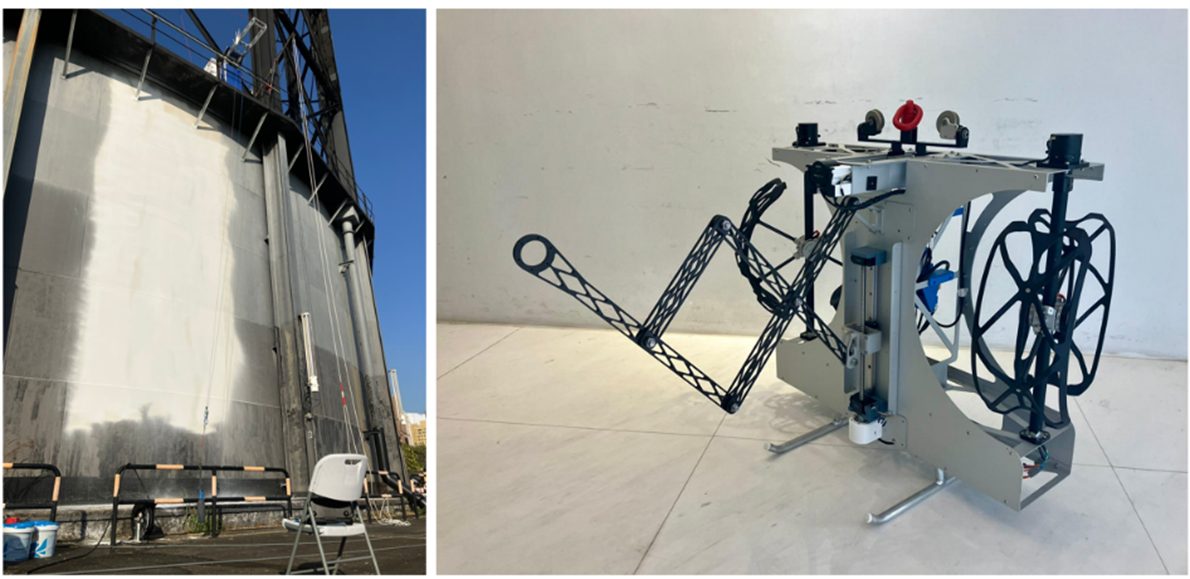
Some of its standout features of RoBosun include:
- Fully autonomous operation and result analysis workflow.
- Lightweight and portable system that can be easily transported to the building rooftop and does not require any fixtures or mounting.
- The robot end-effector can perform works on façade with non-flat wall features protruding of up to 800mm, such as fins, pipes and balconies.
- Physical hammer tapping produces more reliable inspection results with visual and IR approaches to detect concrete spalling.
- System is modular and can be extended to other operations such as painting and cleaning.
As a result of this successful collaboration, the size, weight and function of the robot is able to better match the needs of the industry. Since the original prototype, the robot is at its 4th generation, with new features such as being able to operate on non-flat wall surfaces and ability to stabilise at extended heights of 100m. Through this journey, the robot is now commercialised for real-world use, and has been used at over 25 sites/projects, with clients including the MTR, Hospital Authority, Housing Department, Hong Kong Electric, TownGas and more.
Conclusion
Through these and other project examples, our team believes that such a collaborative development cycle is the path forward to ensure practical and effective solutions that would benefit the building construction industry. Other on-going projects include the development of a robot for bored-pile cleaning, lightweight robot for ceiling void inspection and a lightweight robot for high-ceiling space interior inspection.
|